-
-
-
Clear And Unbiased Facts About Warehouse Management Systems
Within the arena of e-commerce and retail, efficient warehouse fulfillment processes will be the linchpin of success. Warehouse fulfillment encompasses the entire process from receiving orders to preparing them for shipment, ensuring that customers receive their purchases accurately and also on time. This critical area of supply chain management requires meticulous planning, strategic execution, and the usage of advanced technologies to optimize operations. Let’s learn about the significance of warehouse fulfillment and how it drives business success.
1. Order Processing and Management:
Warehouse fulfillment begins with the receipt of customer orders. Efficient order processing involves accurately capturing order details, including product specifications, quantities, and shipping preferences. This information is then entered in to the warehouse management system (WMS), which orchestrates the fulfillment process. Advanced WMS solutions automate order management tasks, prioritize orders determined by predefined criteria for example shipping deadlines or order value, and allocate resources accordingly.2. Inventory Allocation and Pick Lists:
Once orders are processed, the next phase in warehouse fulfillment is inventory allocation. Warehouse staff use pick lists generated by the WMS to locate and retrieve items from designated storage locations. The precision and efficiency of this process will be essential in meeting customer expectations for order accuracy and timely delivery. Utilizing technologies for example barcode scanning and RFID tagging enhances inventory visibility and minimizes errors through the picking process.3. Packing and Shipping Preparation:
After items are picked, they’re brought to the packing area for packaging and shipping preparation. online warehouse fulfillment centers employ standardized packing procedures to make sure that consistency and minimize packaging waste. Automated packing solutions, for example automated carton selection and packing algorithms, optimize packaging efficiency while reducing material costs. On top of that, WMS software generates shipping labels and documentation, streamlining the shipping process and ensuring compliance with carrier requirements.4. Quality Control and Inspection:
Quality control is an integral part of warehouse fulfillment to maintain product quality and customer care. Before orders are shipped, they undergo rigorous inspection to verify product integrity and accuracy. This can include checking for damaged or defective items, verifying order accuracy against pick lists, and ensuring that the packaging meets quality standards. By implementing robust quality control processes, warehouse fulfillment centers can minimize returns and mitigate the risk of negative customer experiences.5. Real-Time Tracking and Reporting:
Visibility into warehouse operations will be important for effective fulfillment management. Advanced WMS solutions provide real-time tracking and reporting capabilities, allowing managers to watch key performance indicators (KPIs) such as order processing times, inventory turnover rates, and fulfillment accuracy. Real-time data insights enable proactive decision making, allowing warehouse managers to identify bottlenecks, optimize workflows, and continuously improve operational efficiency.6. Customer support and Retention:
Ultimately, the goal of warehouse fulfillment is to make sure that customer service and retention. By delivering orders accurately and also on time, warehouse fulfillment centers enhance the overall customer experience and foster loyalty. Timely order fulfillment, transparent communication, and efficient resolution associated with any issues or concerns contribute to positive customer perceptions and repeat business.Warehouse fulfillment is a critical component of supply chain management that directly impacts client satisfaction and business success. By optimizing order processing, inventory management, packing, and shipping processes, warehouse fulfillment centers can streamline operations, minimize costs, and maximize efficiency. Leveraging advanced technologies and continuous process improvement, businesses can stay competitive in today’s dynamic e-commerce landscape and meet the ever-evolving demands of their customers.
- 2024-04-28 1:51 PM
-
Make The Most Out Of This Warehouse Management Systems Information
On this planet of commerce, the journey of a product from production line to consumers hands is as critical as its creation. Shipping products efficiently and effectively is paramount for businesses planning to satisfy customers and uphold their reputation. Whether it is a small artisanal craft or a large-scale industrial component, mastering the art of shipping is important. Here is a comprehensive guide to help navigate the seas of shipping products.
1. Packaging: The journey begins with the packaging. The packaging not just protects the product but additionally serves as its ambassador sales management system during transit. Decide on sturdy materials that will withstand the rigors of transportation while ensuring they’re lightweight to minimize shipping costs. At the same, time, consider eco-friendly options to align with sustainable practices and meet consumer preferences.
2. Deciding on the right Carrier: Selecting the appropriate shipping carrier is pivotal. Factors for example speed, reliability, cost, and destination play a substantial role in the decision. Research various carriers, compare shipping rates, and analyze their track records to seek out the very best fit for your business needs. Furthermore, explore shipping software solutions that integrate with multiple carriers to streamline the process and obtain real-time shipping rates.
3. Labeling and Documentation: Accurate labeling and documentation are important for smooth shipping operations. Make sure that packages are labeled correctly with clear addresses and tracking information. Furthermore, comply with relevant regulations by providing necessary documentation such as customs forms for international shipments. Any discrepancies in labeling or documentation can result in delays or perhaps loss of the shipment.
4. Tracking and Communication: Keep customers informed throughout the shipping process by providing tracking numbers and timely updates. Utilize tracking tools offered by carriers or third-party logistics providers to watch shipments in transit. Effective communication builds trust and enhances the overall customer experience, fostering loyalty and repeat business.
5. Handling Returns: Dealing with returns is definitely an inevitable element of shipping products. Establish clear and hassle-free return policies to facilitate the process for both customers and your team. Streamline reverse logistics operations to inspect, restock, and resell returned items promptly. Embrace returns being an chance to showcase excellent customer support and salvage customer relationships.
6. Continuous Improvement: Regularly evaluate and refine your shipping processes to identify areas for improvement. Solicit feedback from customers regarding their shipping experience and implement necessary changes accordingly. Embrace innovation by exploring emerging technologies for example automation and artificial intelligence to optimize shipping operations further.
Shipping products isn’t merely a logistical task but a critical component of the customer journey. By prioritizing packaging, carrier selection, labeling, tracking, and continuous improvement, businesses can ensure seamless shipping experiences that delight customers and drive long-term success.
- 2024-04-28 1:51 PM
-
The Secret Of Online Warehouse Companies That No One Is Talking About
In recent times, Thailand has emerged as a vibrant hub click here for more info e-commerce, with a expanding digital economy fueled by a tech-savvy population and increasing internet penetration. As online businesses flourish inside this dynamic market, the requirement for efficient fulfillment services has never been greater. Fulfillment services in Thailand offer a selection of approaches to businesses seeking to streamline their operations, expand their reach, and deliver exceptional customer experiences.
Among the key advantages of fulfillment services in Thailand will be the country’s strategic location within the heart of Southeast Asia. Positioned as a regional logistics hub, Thailand offers easy access to neighboring countries such as Malaysia, Singapore, Laos, Cambodia, and Vietnam. This strategic location enables businesses to reach a broader customer base across the region efficiently, tapping into the growing consumer markets of Southeast Asia.
Thailand boasts a robust logistics infrastructure comprising modern transportation networks, state-of-the-art warehousing facilities, and advanced technology systems. Fulfillment providers leverage this infrastructure to offer seamless storage, inventory management, and order fulfillment services to businesses of all sizes. With efficient logistics operations, businesses can minimize shipping times, reduce costs, and deliver products to customers promptly.
Fulfillment services in Thailand are tailored to meet the unique needs of e-commerce businesses operating in the digital marketplace. Providers give a variety of services, including warehousing, inventory management, order processing, picking, packing, and shipping. These comprehensive solutions enable businesses to outsource their logistics operations and concentrate on core activities such as product development, marketing, and customer engagement.
Fulfillment services in Thailand offer scalability and flexibility to accommodate the evolving needs of businesses. Whether a business experiences seasonal fluctuations popular or rapid growth, fulfillment providers can scale their operations accordingly to meet changing requirements. This flexibility allows businesses to adapt quickly to market dynamics without the responsibility of maintaining their own logistics infrastructure.
Thailand serves as an ideal base for businesses looking to expand their reach into international markets. Fulfillment providers in Thailand offer knowledge in international shipping, customs clearance, and compliance, simplifying the complexities of selling products across borders. With access to strategic logistics networks and experienced professionals, businesses can navigate the challenges of global expansion with confidence.
Fulfillment services in Thailand leverage advanced technology answers to optimize warehouse operations and enhance efficiency. Providers utilize warehouse management systems (WMS), automated order processing, barcode scanning, and real-time inventory tracking to streamline processes and minimize errors. By integrating technology into their operations, fulfillment providers offer businesses greater visibility and control over their inventory, ensuring seamless order fulfillment and customer support.
Ultimately, fulfillment services in Thailand prioritize delivering exceptional customer experiences. From branded packaging and customized order tracking to responsive customer support, providers aim to make certain that every interaction with the brand is positive and memorable. By partnering with fulfillment services, businesses can enhance their brand reputation, build customer loyalty, and drive repeat business.
Fulfillment services in Thailand play a pivotal role in supporting the growth of e-commerce businesses in the region. With a strategic location, efficient logistics infrastructure, tailored solutions, scalability, international expansion opportunities, technology integration, as well as a focus on customer experience, fulfillment providers empower businesses to thrive within the digital economy. As Thailand’s e-commerce ecosystem continues to evolve, fulfillment services will remain essential partners for businesses seeking to unlock their full potential in this dynamic market.
- 2024-04-28 1:51 PM
-
Shipping Products Guide
Within the realm of e-commerce and retail, efficient warehouse fulfillment processes are the linchpin of success. Warehouse fulfillment encompasses the entire process from receiving orders to preparing them for shipment, ensuring that customers receive their purchases accurately and also on time. This critical component of supply chain management requires meticulous planning, strategic execution, and the use of advanced technologies to optimize operations. Let’s look into the significance of warehouse fulfillment and the way it drives business success.
1. Order Processing and Management:
Warehouse fulfillment begins with the receipt of customer orders. Efficient order processing involves accurately capturing order details, including product specifications, quantities, and shipping preferences. This data is then entered in to the warehouse management system (WMS), which orchestrates the fulfillment process. Advanced WMS solutions automate order management tasks, prioritize orders based on predefined criteria for example shipping deadlines or order value, and allocate resources accordingly.2. Inventory Allocation and Pick Lists:
Once orders are processed, the next phase in warehouse fulfillment is inventory allocation. Warehouse staff use pick lists generated through the WMS to locate and retrieve items from designated storage locations. The accuracy and efficiency of this process will be very important in meeting customer expectations for order accuracy and timely delivery. Utilizing technologies for example barcode scanning and RFID tagging enhances inventory visibility and minimizes errors throughout the picking process.3. Packing and visit http://www.exchangle.com`s official website Shipping Preparation:
After items are picked, they are brought to the packing area for packaging and shipping preparation. Warehouse fulfillment centers employ standardized packing procedures to make certain consistency and minimize packaging waste. Automated packing solutions, such as automated carton selection and packing algorithms, optimize packaging efficiency while reducing material costs. At the same, time, WMS software generates shipping labels and documentation, streamlining the shipping process and ensuring compliance with carrier requirements.4. Quality Control and Inspection:
Quality control is an integral part of warehouse fulfillment to maintain product quality and customer service. Before orders are shipped, they undergo rigorous inspection to verify product integrity and accuracy. This includes checking for damaged or defective items, verifying order accuracy against pick lists, and ensuring that the packaging meets quality standards. By implementing robust quality control processes, warehouse fulfillment centers can minimize returns and mitigate the risk of negative customer experiences.5. Real-Time Tracking and Reporting:
Visibility into warehouse operations is crucial for effective fulfillment management. Advanced WMS solutions provide real-time tracking and reporting capabilities, allowing managers to monitor key performance indicators (KPIs) for example order processing times, inventory turnover rates, and fulfillment accuracy. Real-time data insights enable proactive decision-making, allowing warehouse managers to identify bottlenecks, optimize workflows, and continuously improve operational efficiency.6. Customer satisfaction and Retention:
Ultimately, the goal of warehouse fulfillment is to make sure customer care and retention. By delivering orders accurately as well as on time, warehouse fulfillment centers enhance the overall customer experience and foster loyalty. Timely order fulfillment, transparent communication, and efficient resolution of any issues or concerns contribute to positive customer perceptions and repeat business.Warehouse fulfillment is a critical component of supply chain management that directly impacts client satisfaction and business success. By optimizing order processing, inventory management, packing, and shipping processes, warehouse fulfillment centers can streamline operations, minimize costs, and maximize efficiency. Leveraging advanced technologies and continuous process improvement, businesses can stay competitive in today’s dynamic e-commerce landscape and meet the ever-evolving demands of their customers.
- 2024-04-28 1:51 PM
-
Seven Warehouse Management Systems Secrets You Never Knew
In the intricate dance of modern commerce, where products traverse the globe at a dizzying pace, efficient warehouse management systems (WMS) will be the unsung heroes behind the scenes. These systems orchestrate the flow of goods, optimize storage space, and synchronize logistics operations, enabling businesses to meet customer demands promptly and maintain a competitive edge. Let’s look into the world of WMS and explore their significance in today’s supply chain landscape.
1. Definition and Functionality:
A Warehouse Management System (WMS) is a software application designed to control and manage warehouse operations efficiently. Its functionalities typically include inventory management, order fulfillment, receiving and put-away, picking and packing, shipping, and real-time monitoring of warehouse activities. WMS software utilizes a mix of barcode scanning, RFID technology, and sophisticated algorithms to streamline processes and enhance productivity.2. Inventory Accuracy and Optimization:
Among the primary functions of WMS is maintaining accurate inventory records. By tracking every movement of goods in real-time, WMS guarantees that inventory levels are up-to-date, minimizing stockouts and overstock situations. Aside from that, WMS employs intelligent algorithms to optimize inventory placement within the warehouse, reducing unnecessary travel time and maximizing storage space utilization.3. Order Fulfillment Efficiency:
WMS plays a pivotal role in expediting order fulfillment processes. It orchestrates the picking, packing, and shipping of orders with precision and speed. Through advanced features such as wave picking, batch picking, and zone picking, WMS optimizes picking routes and assigns tasks to warehouse staff systematically, reducing picking errors and increasing throughput.4. Enhanced Visibility and Traceability:
Visibility and traceability are paramount in today’s supply chain environment. WMS provides real-time visibility into warehouse operations, allowing managers to monitor inventory levels, track order statuses, and identify bottlenecks proactively. Also, WMS enables traceability by recording more information about each product’s movement, from receipt to dispatch, facilitating compliance with regulatory requirements and ensuring product quality and safety.5. Labor Management and Resource Optimization:
Effective labor management will be important for maintaining warehouse efficiency. WMS helps optimize workforce utilization by providing insights into labor productivity, task allocation, and satisfaction tracking. By identifying areas for improvement and implementing labor management strategies, businesses can minimize labor costs while maximizing operational output.6. Integration and Scalability:
WMS software often integrates seamlessly with other enterprise systems such as Enterprise Resource Planning (ERP), Transportation Management Systems (TMS), and Customer Relationship sales management system (look here) (CRM) platforms. This integration enables data sharing and process automation across the supply chain, fostering collaboration and driving efficiency. Furthermore, modern WMS solutions are scalable, allowing businesses to adapt to evolving needs and expand their operations seamlessly.7. Continuous Improvement and Innovation:
The landscape of warehouse management is continuously evolving, driven by technological advancements and changing market dynamics. Leading-edge WMS solutions leverage emerging technologies for example Artificial Intelligence (AI), Internet of Things (IoT), and machine learning to further enhance efficiency and adaptability. By embracing innovation and fostering a culture of continuous improvement, businesses can stay in advance of the curve and unlock new opportunities for growth.Warehouse Management Systems play a pivotal role in optimizing warehouse operations and driving supply chain efficiency. From inventory accuracy and order fulfillment to labor management and scalability, WMS solutions empower businesses to meet customer demands swiftly as well as manage a competitive edge in today’s dynamic marketplace. As technology continues to advance, the role of WMS will only become more indispensable in shaping the future of logistics and commerce.
- 2024-04-28 1:46 PM
-
What Everybody Dislikes About Warehouse Management Services And Why
In the world of commerce, the journey of a product from production line to consumers hands is as critical as its creation. Shipping products efficiently and effectively is paramount for businesses planning to satisfy customers and uphold their reputation. Whether it is a small artisanal craft or a large-scale industrial component, mastering the art of shipping is important. Here’s a comprehensive guide to help navigate the seas of shipping products.
1. Packaging: The journey begins with the packaging. The packaging not only protects the product but additionally serves as its ambassador during transit. Select sturdy materials that may withstand the rigors of transportation while ensuring they can be lightweight to minimize shipping costs. Furthermore, consider eco-friendly options to align with sustainable practices and meet consumer preferences.
2. Picking the right Carrier: Selecting the appropriate shipping carrier is pivotal. Factors such as speed, reliability, cost, and destination play a vital role inside this decision. Research various carriers, compare shipping rates, and analyze their track records to search out the most effective fit for your business needs. What’s more, explore shipping software solutions that integrate with multiple carriers to streamline the process and obtain real-time shipping rates.
3. Labeling and Documentation: Accurate labeling and documentation shall be important for smooth shipping operations. Ensure that packages are labeled correctly with clear addresses and tracking information. Additionally, comply with relevant regulations by providing necessary documentation such as customs forms for international shipments. Any discrepancies in labeling or documentation can lead to delays and even loss of the shipment.
4. Tracking and Communication: Keep customers informed through the shipping process by providing tracking numbers and timely updates. Utilize tracking tools provided by carriers or third-party logistics providers to watch shipments in transit. Effective communication builds trust and enhances the overall customer experience, sales management system [visit the next page] fostering loyalty and repeat business.
5. Handling Returns: Going through returns is an inevitable aspect of shipping products. Establish clear and hassle-free return policies to facilitate the process for both customers and your team. Streamline reverse logistics operations to inspect, restock, and resell returned items promptly. Embrace returns being an chance to showcase excellent customer service and salvage customer relationships.
6. Continuous Improvement: Regularly evaluate and refine your shipping processes to identify areas for improvement. Solicit feedback from customers regarding their shipping experience and implement necessary changes accordingly. Embrace innovation by exploring emerging technologies for example automation and artificial intelligence to optimize shipping operations further.
Shipping products just isn’t merely a logistical task but a critical component of the customer journey. By prioritizing packaging, carrier selection, labeling, tracking, and continuous improvement, businesses can ensure seamless shipping experiences that delight customers and drive long-term success.
- 2024-04-28 1:46 PM
-
What Everyone Is Saying About Online Warehouse Websites And What You Should Do
Lately, Thailand has emerged as a vibrant hub for e-commerce, with a rapidly growing digital economy fueled by a tech-savvy population and increasing internet penetration. As online businesses flourish in this particular dynamic market, the interest in efficient fulfillment services has never been greater. Fulfillment services in Thailand offer a variety of answers to businesses seeking to streamline their operations, expand their reach, and deliver exceptional customer experiences.
One of the key advantages of fulfillment services in Thailand will be the country’s strategic location in the heart of Southeast Asia. Positioned as a regional logistics hub, Thailand offers easy access to neighboring countries for example Malaysia, Singapore, Laos, Cambodia, and Vietnam. This strategic location enables businesses to reach a broader customer base across the region efficiently, tapping in to mouse click the following web site growing consumer markets of Southeast Asia.
Thailand boasts a robust logistics infrastructure comprising modern transportation networks, state of the art warehousing facilities, and advanced technology systems. Fulfillment providers leverage this infrastructure to offer seamless storage, inventory management, and order fulfillment services to businesses of all sizes. With efficient logistics operations, businesses can minimize shipping times, reduce costs, and deliver products to customers promptly.
Fulfillment services in Thailand are tailored to meet the unique needs of e-commerce businesses operating in the digital marketplace. Providers provide a selection of services, including warehousing, inventory management, order processing, picking, packing, and shipping. These comprehensive solutions enable businesses to outsource their logistics operations and focus on core activities for example program development, marketing, and customer engagement.
Fulfillment services in Thailand offer scalability and flexibility to accommodate the evolving needs of businesses. Whether a business experiences seasonal fluctuations in demand or rapid growth, fulfillment providers can scale their operations accordingly to meet changing requirements. This flexibility allows businesses to adapt quickly to market dynamics without the responsibility of maintaining their very own logistics infrastructure.
Thailand serves as an ideal base for businesses looking to expand their reach into international markets. Fulfillment providers in Thailand offer knowledge in international shipping, customs clearance, and compliance, simplifying the complexities of selling products across borders. With access to strategic logistics networks and experienced professionals, businesses can navigate the challenges of global expansion with confidence.
Fulfillment services in Thailand leverage advanced technology approaches to optimize warehouse operations and enhance efficiency. Providers utilize warehouse management systems (WMS), automated order processing, barcode scanning, and real-time inventory tracking to streamline processes and minimize errors. By integrating technology into their operations, fulfillment providers offer businesses greater visibility and control over their inventory, ensuring seamless order fulfillment and customer service.
Ultimately, fulfillment services in Thailand prioritize delivering exceptional customer experiences. From branded packaging and customized order tracking to responsive customer support, providers try to make certain that every interaction with the brand is positive and memorable. By partnering with fulfillment services, businesses can enhance their brand reputation, build customer loyalty, and drive repeat business.
Fulfillment services in Thailand play a pivotal role in supporting the expansion of e-commerce businesses within the region. With a strategic location, efficient logistics infrastructure, tailored solutions, scalability, international expansion opportunities, technology integration, and also a focus on customer experience, fulfillment providers empower businesses to thrive in the digital economy. As Thailand’s e-commerce ecosystem continues to evolve, fulfillment services will remain essential partners for businesses seeking to unlock their full potential inside this dynamic market.
- 2024-04-28 1:44 PM
-
What Everybody Else Does When It Comes To Online Warehouse Systems And What You.
In Read the Full Post world of retail and e-commerce, efficient storage and shipping of products are essential for meeting customer demands and maintaining a competitive edge. Businesses must implement effective strategies to ensure that their inventory is stored securely and shipped promptly to customers. Below are a few key things to consider for optimizing the storing and shipping process:
1. Inventory Management:
Efficient storage begins with effective inventory management. Businesses should implement systems to track inventory levels accurately, monitor product movement, and forecast demand. By maintaining optimal inventory levels, businesses can minimize storage costs while ensuring that products are readily available to satisfy orders.2. Organized Warehouse Layout:
A well-organized warehouse layout is important for maximizing storage space and facilitating efficient order picking. Businesses should design their warehouse layout to optimize space utilization, minimize travel time for workers, and streamline the flow of products from receiving to shipping areas. This will likely be achieved through strategies such as vertical storage, aisle optimization, and logical product grouping.3. Proper Packaging:
Proper packaging is crucial for protecting products during storage and transit. Businesses should invest in high-quality packaging materials that provide adequate protection against damage, moisture, as well as other hazards. Moreover, packaging should be designed to optimize space utilization and minimize shipping costs without compromising product safety.4. Just-In-Time Inventory:
Implementing a just-in-time (JIT) inventory strategy can certainly help businesses reduce storage costs and minimize excess inventory. By closely aligning inventory levels with demand forecasts, businesses can replenish stock as needed, minimizing the necessity for large storage facilities and reducing the risk of overstocking.5. Efficient Shipping Practices:
Streamlining the shipping process is essential for delivering products to customers promptly and cost-effectively. Businesses should partner with reliable shipping carriers and negotiate favorable rates to minimize shipping costs. What’s more, implementing automated shipping processes, such as batch processing and order routing, will help businesses fulfill orders quickly and accurately.6. Order Fulfillment Optimization:
Optimizing order fulfillment processes is crucial for ensuring timely delivery of products to customers. Businesses should implement efficient order picking, packing, and shipping processes to minimize turnaround times and reduce the risk of shipping errors. Utilizing technology such as barcode scanning and automated sorting systems might help streamline order fulfillment operations and improve accuracy.7. Continuous Improvement:
Continuous improvement is key to optimizing storing and shipping processes. Businesses should regularly review and evaluate their storage and shipping practices to identify areas for improvement and implement strategies to address inefficiencies. By adopting a mindset of continuous improvement, businesses can stay ahead of the competition and deliver exceptional service to customers.Efficient storing and shipping of products are critical for businesses to ensure success in today’s competitive marketplace. By implementing strategies such as effective inventory management, organized warehouse layout, proper packaging, and efficient shipping practices, businesses can optimize their storing and shipping processes, minimize costs, and deliver a superior customer experience.
- 2024-04-28 1:42 PM
-
Basic Guidance For You In Relation To Warehouse Fulfillments
In the realm of e-commerce and retail, efficient warehouse fulfillment processes will be the linchpin of success. Warehouse fulfillment encompasses the entire process from receiving orders to preparing them for shipment, ensuring that customers receive their purchases accurately as well as on time. This critical facet of supply chain management requires meticulous planning, strategic execution, as well as the use of advanced technologies to optimize operations. Let’s explore the significance of warehouse fulfillment and just how it drives business success.
1. Order Processing and Management:
Warehouse fulfillment begins with the receipt of customer orders. Efficient order processing involves accurately capturing order details, including product specifications, quantities, and shipping preferences. This data is then entered in to the warehouse management system (WMS), which orchestrates the fulfillment process. Advanced WMS solutions automate order management tasks, prioritize orders according to predefined criteria such as shipping deadlines or order value, and allocate resources accordingly.2. Inventory Allocation and Pick Lists:
Once orders are processed, the next step in warehouse fulfillment is inventory allocation. Warehouse staff use pick lists generated through the WMS to locate and retrieve items from designated storage locations. The precision and efficiency of this process will be crucial in meeting customer expectations for order accuracy and timely delivery. Utilizing technologies such as barcode scanning and RFID tagging enhances inventory visibility and minimizes errors during the picking process.3. Packing and Shipping Preparation:
After items are picked, they are brought to the packing area for packaging and shipping preparation. Warehouse fulfillment centers employ standardized packing procedures to make certain consistency and minimize packaging waste. Automated packing solutions, for example automated carton selection and packing algorithms, optimize packaging efficiency while reducing material costs. Likewise, WMS software generates shipping labels and documentation, streamlining the shipping process and ensuring compliance with carrier requirements.4. Quality Control and Inspection:
Quality control is definitely an integral part of warehouse fulfillment to maintain product quality and customer service. Before orders are shipped, they undergo rigorous inspection to verify product integrity and accuracy. This can include checking for damaged or defective items, verifying order accuracy against pick lists, and ensuring that the packaging meets quality standards. By implementing robust quality control processes, warehouse fulfillment centers can minimize returns and mitigate the risk of negative customer experiences.5. Real-Time Tracking and Reporting:
Visibility into warehouse operations is important for effective fulfillment management. Advanced WMS solutions provide real-time tracking and reporting capabilities, allowing managers to monitor key performance indicators (KPIs) for example order processing times, inventory turnover rates, and fulfillment accuracy. Real-time data insights enable proactive decision making, allowing warehouse managers to identify bottlenecks, optimize workflows, and continuously improve operational efficiency.6. Client satisfaction and Retention:
Ultimately, the goal of warehouse fulfillment is to make sure client satisfaction and retention. By delivering orders accurately as well as on time, warehouse Fulfillment service (you could try this out) centers enhance the overall customer experience and foster loyalty. Timely order fulfillment, transparent communication, and efficient resolution of any issues or concerns contribute to positive customer perceptions and repeat business.Warehouse fulfillment is a critical component of supply chain management that directly impacts customer care and business success. By optimizing order processing, inventory management, packing, and shipping processes, warehouse fulfillment centers can streamline operations, minimize costs, and maximize efficiency. Leveraging advanced technologies and continuous process improvement, businesses can stay competitive in today’s dynamic e-commerce landscape and meet the ever-evolving demands of their customers.
- 2024-04-28 1:39 PM
-
The 4 Secrets About Warehouse Management Systems Only A Small Number Of People.
On this planet of commerce, the journey of a product from production line to consumers hands is as critical as its creation. Shipping products efficiently and effectively is paramount for businesses aiming to satisfy customers and uphold their reputation. Whether it is a small artisanal craft or Warehouse Fulfillment (Exchangle said) perhaps a large-scale industrial component, mastering the art of shipping will be essential. Here’s a comprehensive guide to help navigate the seas of shipping products.
1. Packaging: The journey begins with the packaging. The packaging not simply protects the product but also serves as its ambassador during transit. Decide on sturdy materials that may withstand the rigors of transportation while ensuring they’re lightweight to minimize shipping costs. At the same, time, consider eco-friendly options to align with sustainable practices and meet consumer preferences.
2. Deciding on the right Carrier: Selecting the appropriate shipping carrier is pivotal. Factors for example speed, reliability, cost, and destination play a significant role within this decision. Research various carriers, compare shipping rates, and analyze their track records to locate the best fit for your business needs. Also, explore shipping software solutions that integrate with multiple carriers to streamline the process and obtain real-time shipping rates.
3. Labeling and Documentation: Accurate labeling and documentation will be very important for smooth shipping operations. Ensure that packages are labeled correctly with clear addresses and tracking information. What’s more, comply with relevant regulations by providing necessary documentation such as customs forms for international shipments. Any discrepancies in labeling or documentation can lead to delays or maybe loss of the shipment.
4. Tracking and Communication: Keep customers informed through the shipping process by providing tracking numbers and timely updates. Utilize tracking tools provided by carriers or independent party logistics providers to watch shipments in transit. Effective communication builds trust and enhances the overall customer experience, fostering loyalty and repeat business.
5. Handling Returns: Dealing with returns is an inevitable facet of shipping products. Establish clear and hassle-free return policies to facilitate the process for both customers as well as your team. Streamline reverse logistics operations to inspect, restock, and resell returned items promptly. Embrace returns as an chance to showcase excellent customer support and salvage customer relationships.
6. Continuous Improvement: Regularly evaluate and refine your shipping processes to identify areas for improvement. Solicit feedback from customers regarding their shipping experience and implement necessary changes accordingly. Embrace innovation by exploring emerging technologies such as automation and artificial intelligence to optimize shipping operations further.
Shipping products just isn’t merely a logistical task but a critical component of the customer journey. By prioritizing packaging, carrier selection, labeling, tracking, and continuous improvement, businesses can ensure seamless shipping experiences that delight customers and drive long-term success.
- 2024-04-28 1:38 PM
-
有名人
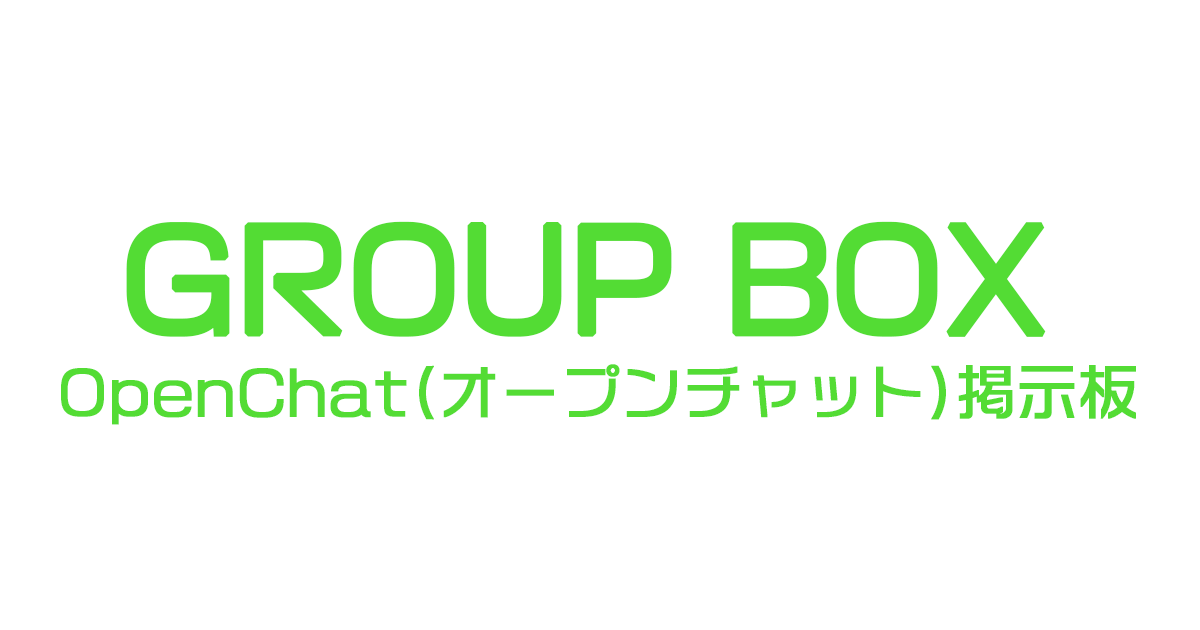
掲示板
arc’teryx clothing,
blog topic