-
-
-
Plinko kasyno online – prosta i emocjonująca rozrywka z dodatkowymi szansami.
Plinko stanowi najbardziej spośród fajnych zabaw na serwisach platformach hazardowych online. Ta właśnie gra bazuje na łatwych zasadach, lecz zapewniają wielką dawkę emocji plus okazję na nagrody. Gra Plinko pochodzi z oryginalnego programu telewizyjnego, w czasie kulki spadające na tablicę z kołkami wpływały o wygranych. W serwisie webpage mechanika został dostosowana na potrzeby gier hazardowych, budując nowoczesną rozrywkę dostępną dla dla każdego, ten, co lubi zadania i ruchliwą rozgrywkę. Popularność plinko kasyno rośnie z dnia na dzień z powodu prostocie gry, szybkości oraz opcjom obstawiania wielu efektów. Ludzie grający cenią sobie możliwość korzystania z kasyno plinko online, co oznacza że nie muszą nie powinni wyjść z domu, aby przeżyć emocji. Trzeba dodać, że plinko kasyno to nie jedynie gra, a także metoda by sprawdzić swoich zdolności przewidywania oraz zarządzania ryzykiem. Kasyno Plinko otrzymało liczne grono wielbicieli także bo gra jest łatwa do zrozumienia, i zarazem ma duże możliwości nagrody. Stanowi to fajne dla tych, co startują swoją drogę w kasynach w sieci. Ponadto, recenzje Plinko wśród graczy są pozytywne, co świadczy o tym, że gra spełnia oczekiwania i dostarcza mnóstwo zabawy. Z tego powodu liczne serwisy decyduje się na wprowadzenie kasyno plinko do swojego portfolio gier. Opcja gry na różne stawki i elastyczność zasad sprawiają, że Plinko w sieci można grać dla graczy czasem grających, a także dla graczy zaawansowanych. Podsumowując, plinko kasyno jest dobrym mixem tradycji z nowoczesnością, co przyciąga więcej fanów gier hazardowych. Geneza Plinko pochodzi w popularnym amerykańskim programie w show „The Price is Right”, gdzie Plinko była główną atrakcją. W oryginalnej wersji, ludzie wpuszczali pionową kulkę na planszę wypełnioną kołkami, a ruch kulki mówił o nagrodzie. Sukces tej łatwej ale wciągającej mechaniki doprowadził do tego, że niedługo pojawiły się próby adaptacji gry do sieci i kasyn w sieci. Dostosowanie Plinko na serwisy hazardowe wystartowała kilka lat temu, wraz z rozwojem technologii internetowej i wzrastającym popytem prostymi, lecz emocjonującymi grami kasynowymi. W odróżnieniu od klasycznych automatów, Kasyno Plinko daje inną mechanikę, która nie jest tylko losowa, a także na kontakcie z grą. Początkowo dostępne były tylko proste wersje, jednak z czasem twórcy oprogramowania wprowadzili wiele udogodnień i wariantów, co uczyniło grę ciekawszą. Kasyno Plinko w sieci zaczęło pojawiać się na serwisach z nowoczesnymi grami, co przyciągnęło dużą grupę użytkowników szukających nowości. Wrażenia graczy poprawiły się szybko, co dodatkowo motywowało operatorów do pracy nad grą. W efekcie powstały różnorodne wersje kasyno plinko, różniły się wyglądem, stawkami i regułami, lecz miały ten sam spadający element. Dynamiczny rozwój technologii mobilnych umożliwił także dostęp do plinko kasyno online na urządzeniach mobilnych, co znacznie zwiększyło popularność gry. Dzięki temu plinko kasyno stało się jedną z ulubionych pozycji w rankingach gier w Polsce i na świecie.
Gra Plinko to zabawa oparta w oparciu o prostych przepisach, jednakże zawierają w treści mnóstwo strategii a także emocji. Generalnie, rozgrywka polega na tym, kiedy zawodnik zaznacza punkt, w którym puści kulkę na powierzchni tablicy zapełnionej stykami, a następnie kulka odbija się od nich i ląduje w jedno z licznych krat na dole. Wszystkie pole ma przypisaną ustaloną sumę zysku bądź kurs. Misją jest uderzenie piłeczką do pola najbardziej wartościowe, co pozwala uzyskać większy zysk. Kasyno plinko opiera się na losowości odbicia kuli, jednak mądre ustawienie pozycji początkowej może zwiększyć prawdopodobieństwo trafienia w bardziej opłacalne pola. W plinko kasyno online można znaleźć wiele wersji rozgrywki, gdzie liczba kołków, rozmiar planszy jak i stawki mogą się różnić. Jednak bazowa mechanika jest stała – ta zachęca graczy, gdyż daje możliwość kontroli nad efektem i pozwala na analizę decyzji. Kasyno plinko online zazwyczaj daje także możliwość zmiany ryzyka – można obstawiać bezpieczniejsze miejsca z mniejszymi mnożnikami albo podjąć ryzyko trafienie na pola z większymi nagrodami. Gracze, poszukujący większej interakcji, docenią to, że w plinko kasyno można podejmować decyzje dotyczące strategii i wysokości zakładu. To odróżnia tę grę od klasycznych automatów, które są całkowicie losowe. Mechanika plinko kasyno jest też bardzo przejrzysta i łatwa do zrozumienia, dzięki temu nowi gracze łatwo ją łapią. Co więcej, GUI gry online jest zwykle przyjazny i ładny, co sprawia że gra plinko online stanowi dobrą opcję dla osób lubiących hazard, którzy cenią sobie prostotę i szybkie emocje. Plinko w kasynie online jest dziś dostępne w wielu wariantach, dostosowanych do różnych gustów i wymagań graczy. Twórcy gier stają się nieustannie doskonalą swoje produkty, prezentując odmienne wersje tej modnej gry, które różnią się nie tylko wyglądem, a także regułami oraz skomplikowaniem. Najpopularniejsze kasyno plinko to tradycyjne wersje, które trzymają się bazowej mechaniki spadającej kuli i kołków, jak i wersje z dodatkami z dodatkowymi funkcjami i bonusami. Wśród typów plinko można wyróżnić gry o różnej liczbie pól i styków, które wpływają na dynamikę rozgrywki. Istnieją też wersje, w których zamiast standardowych pól z mnożnikami, są bonusy, darmowe rundy albo inne wygrane. Popularnym rozwiązaniem są także plinko kasyno dające różne stopnie ryzyka – od niskiego ryzyka z małymi mnożnikami, dla wariantów dla graczy gotowych na większe wyzwania i wyższe nagrody. Kasyno plinko w sieci zwykle umożliwia rozgrywkę multiplayer lub turnieje, co podnosi interakcję między zawodnikami i podnosi poziom emocji. Z tego powodu zabawa nie nudzi i ciągle przyciąga nowych użytkowników. Warto dodać, że różne serwisy proponują różne style i nastrój gry – od prostych i jasnych interfejsów po barwne i bogate wersje. Każdy gracz może zatem wybrać kasyno plinko, które odpowiada jego upodobaniom.
Plinko kasyno to zabawa, która ma wiele zalet, dzięki którym zdobywa wzrastającą popularność wśród graczy kasyn internetowych. Najważniejsze, jest niezwykle łatwa, co powoduje, że nawet początkujący gracze mogą łatwo zacząć zabawę z kasyno plinko bez konieczności poznawania trudnych reguł. W tym samym czasie gra ta jest dynamiczna i pasjonująca, co ciągnie fanów szukające szybkiej zabawy i możliwości wygranej. Kolejną zaletą kasyno plinko jest możliwość grania – można uczestniczyć prawie o dowolnej godzinie dnia i nocy, korzystając z smartfonów lub laptopów. Brak skomplikowanych procedur i szybki przebieg rozgrywki to wielkie atuty dla użytkowników, które chcą uczestniczyć w szybkie rundy lub w między innymi aktywnościami. Ponadto, kasyno plinko posiada szeroką gamę stawek, co oznacza, że można rozpocząć zabawę z małym kapitałem, a także ryzykować większe sumy, gdy ma się ochotę na większe emocje. Komentarze graczy (kasyno plinko opinie) potwierdzają, że ta gra jest naprawdę zajmująca i przynosi radość z gry. Wielu użytkowników docenia czytelny wygląd oraz to, że można w pewnym stopniu kontrolować wynik, decydując, gdzie puścić kulkę. Dzięki temu gra w plinko kasyno nie jest czysto losowa, co wyróżnia ją na tle konkurencyjnych tytułów. Na dodatek, plinko kasyno online często oferuje promocje i bonusy, które pomagają wygrać i wydłużają zabawę. Kasyno plinko opinie są istotnym sygnałem dla świeżych użytkowników, zastanawiających się, czy próbować. Przeważająca liczba opinii zwraca uwagę na łatwość i tempo gry jako główne atuty plinko kasyno. Gracze pozytywnie oceniają unikalną mechanikę, która łączy elementy losowości z możliwością podejmowania decyzji, co sprawia, że gra jest bardziej angażująca niż klasyczne sloty. Spora grupa graczy podkreśla, że kasyno plinko online to dobra opcja dla osób szukających czegoś nowego i nowego w kasynach. Wśród negatywnych opinii zdarzają się oskarżenia o nadmierny przypadek i braku możliwości stosowania zaawansowanych strategii, jednak są sporadyczne. Kasyno plinko opinie wskazują, że gra jest raczej przeznaczona do rozrywki niż do zarabiania dużych pieniędzy, co dla dużo osób jest atutem.
Opinie użytkowników zwykle wskazują też o fajny wygląd oraz intuicyjny panel Plinko casino internetowe, jakie pomagają obsługę na zabawy dla licznych sprzętach. Krótko mówiąc, Plinko casino recenzje w kręgu społeczności graczy są przede wszystkim pozytywne. Gracze cenią tą rozgrywkę ze względu na możliwość błyskawicznej gry, silne uczucia jak również elastyczne nastawienie w kwestii zakładów. To z tego powodu sprawia, że właśnie plinko kasyno w sieci ma rosnącą sławę oraz staje się częścią ulubionych opcji w różnych serwisach hazardowych. Choć plinko kasyno stanowi rozgrywka głównie zależna od przypadku, są kilka sposobów jak również rad, co mogą ułatwić zwiększyć prawdopodobieństwo do sukces. Pierwszą rzeczą jest, warto zwrócić uwagę na dobór lokacji, tam, piłka bywa upuszczana – choć rezultat bywa w pewnym stopniu przypadkowy, kilka strefy dają szansę lepsze szansę odbic prowadzących do zwycięstwa. Analiza minionych gier oraz analiza ruchów piłki da się wspierać przy lepszym zrozumieniu mechaniki i wyborze najlepszej strategii. Drugą kluczową wskazówką jest zarządzanie budżetem. W kasyno plinko recenzje najczęściej podkreślają, że też rozsądne gospodarowanie pieniędzmi jak również niestawianie przesadnych stawki umożliwia bardziej dłużej trwającą oraz lepszą grę. Dobrym pomysłem jest ustalić własny maksimum, ten nie będzie przekraczany, żeby gra była rozrywką, a nie była źródłem nerwów. Jeszcze , kasyno plinko w sieci ma liczne stopnie zagrożenia, dlatego warto dopasować zakłady w zależności od własnych gustów oraz praktyki. Kolejną strategią to korzystanie dostępnych nagrod i akcji. Wiele plinko casino w sieci daje dodatki dla nowych bądź bezpłatne spiny, co poprawiają szanse w zysk bez potrzeby inwestowania własnych pieniędzy. Uważne przeglądanie zasad jak również wykorzystywanie tych promocji stanowi drogę w skuteczniejszą grę. Ostatecznie, kluczowe jest, by bawić się odpowiedzialnie jak również delektować się grą, co jest głównym funkcją Plinko casino. Bezpieczeństwo jest ważny aspekt wszystkich zabawy kasynowej online, a plinko casino internetowe nie bywa w tym miejscu odstępstwem. Ważne to, by dobierać wyłącznie pewne i licencjonowane platformy, jakie dają fair grę i zabezpieczenie osobowych. Plinko casino, co działa legalnie, używa opierając się na zatwierdzonych generatorów liczb losowych (RNG), co sprawia, że gwarantuje, że właśnie rezultaty bywają w pełni przypadkowe oraz nie da się ich oszukać. W rezultacie ludzie posiadają pewność, że ich zyski są rzeczywiste, jak również gra przebiega w sposób jasny sposób. W plinko kasyno recenzje często zaznaczają, że właśnie rzetelność to kluczowym głównych atutów tej, kiedy jest oferowana na znane kasyno online. Operatorzy troszczą się o aby , aby każde operacje są zabezpieczone oraz realizowane bez opóźnień a także łatwo. Dodatkowo, mnóstwo serwisów ma opcje do ograniczeń oraz ustalania limitów pieniędzy, co umożliwia wspiera ludziom utrzymywać odpowiedzialne postawę wobec gry. Warto wziąć pod uwagę, że właśnie Plinko casino w internecie to formą spędzania czasu, a nie jest nie metoda do błyskawiczne zarobek, z tego powodu niezależnie należy grać stosując umiarem i rozważnie. Bezpieczeństwo jak również bezpieczeństwo w kontekście plinko kasyno to podstawy, co wpływają na trafnych wrażeniach ludzi jak również stabilności segmentu gier gamblerskich w sieci.
Oferty oraz promocje to jednym z kluczowych czynników, za sprawą których liczni osób postanawia uczestniczyć w zabawę w online kasyno. Dostawcy regularnie proponują rozmaite bonusy powitalne, gratisowe spiny czy programy punktowe, a które zwiększają prawdopodobieństwo wygranej oraz pozwalają dłuższe granie za ten sam budżet. Kasyno plinko wykorzystuje fakt, że to, ciekawe oferty ciągną nowych graczy jak również skłaniają do częstej gry. By skorzystać z bonusów, należy uważnie zapoznać się z ich warunkami – często należy spełnić spełnienie określonych wymagań obrotu bądź minimalną stawkę. Opinie o kasynie plinko zaznaczają, że właśnie wykorzystywanie ofert jest dobry sposób na poprawę wygranych, gdy użytkownik przestrzega zasad. Najlepiej korzystać z dedykowanych ofert specjalnie dla gier plinko, co poprawiają efekty płynące z promocji. Dobrze jest też obserwowaniu nowych promocji i okazjonalnych bonusów, co pomagają podnieść interes gry. Dzięki temu kasyno plinko online jest bardziej żywe oraz ciekawe, a rozgrywka zyskuje nowy wymiar. Bonusy nie tylko dodatkowa gotówka, ale i droga do poznania różnych wersji plinko i rozwijanie swoich umiejętności bez utraty własnych pieniędzy.
Plinko kasyno online ma przed sobą bardzo obiecującą przyszłość. Tendencje na rynku gier hazardowych wskazują, że właśnie łatwość, krótka zabawa a także specyficzny system będą nadal ważnymi częściami przyciągającymi nowych graczy. Producenti inwestują w rozwój technologii, co pozwala robienie lepszych wersji plinko kasyno, z ulepszoną grafiką, funkcjami interaktywnymi oraz możliwością integracji z rzeczywistością wirtualną czy rozszerzoną. Kolejnym trendem jest większe znaczenie urządzeń mobilnych – kasyno plinko w sieci jest już na telefonach, ale w przyszłości pojawią się lepsze wersje, pozwalające grać gdziekolwiek i kiedykolwiek. Również rozwój sztucznej inteligencji może wpłynąć na sposób, w jaki użytkownicy myślą i planują ruchy w kasynie plinko, pozwalając na dopasowane doświadczenia. Wreszcie, uczciwość i jasność mają większe znaczenie, w kasynach, dzięki czemu kasyno plinko musi mieć wyższe normy bezpieczeństwa i zasad. W odpowiedzi na te potrzeby tworzą się nowe technologie, które jeszcze bardziej zabezpieczą graczy i podnoszą wiarygodność kasyn. Dzięki temu przyszłość plinko kasyno jest jasna, i ta gra może być kluczowa w świecie gier online.
Strona internetowa: https://www.iddp.eng.ku.ac.th/3rd-year-iddp-students-visit-aerospace-industry-in-singapore/
FAQ
Jak działa plinko kasyno? Plinko kasyno to gra internetowa, oparta na mechanice spadającej kulki, która odbija się od kołków na planszy i trafia na pole z wygraną. Gra ma prostą mechanikę i element losowości z możliwością podejmowania decyzji przez gracza, co czyni ją atrakcyjną dla wielu graczy.
Czy kasyno plinko online to bezpieczna gra? Zgadza się, jeśli wybierzesz legalne i sprawdzone kasyno. Te strony mają certyfikowane generatory losowe i chronią dane graczy, zapewniając uczciwą i transparentną rozgrywkę.
Jakie są triki do plinko kasyno? Choć gra ma losowy element, warto śledzić tor kulki i wybierać optymalne miejsce jej upuszczenia. Zarządzanie budżetem oraz używanie bonusów także zwiększa szanse.
Jakie są opinie graczy na temat kasyno plinko? Ogólnie opinie są pozytywne. Doceniana jest prostota, szybkie tempo gry i to, że mogą wybrać miejsce startu kulki. Słabsze strony dotyczą głównie losowości wyników, co jest normalne w hazardzie.
Czy w plinko kasyno można grać na urządzeniach mobilnych? Jasne, prawie każde kasyno plinko działa na telefonach i tabletach, co umożliwia grę w dowolnym miejscu i czasie, zachowując pełną funkcjonalność i komfort rozgrywki.
- 2025-07-19 3:38 AM
-
oline casino Lev 79y
<br>Казино Лев: Ваш путь к азарту и большим выигрышам!
Казино Лев — это современная игровая платформа, созданная специально для русскоговорящих игроков, которые ценят качественные азартные развлечения, щедрые бонусы и надёжность. С лицензией Кюрасао (Avento N.V. №1668/JAZ) и более чем тысячей игр от ведущих мировых провайдеров, Казино Лев стало настоящей находкой для любителей азарта. Официальный сайт clubs-lev.org предлагает удобный интерфейс, безопасные транзакции и массу возможностей для яркого отдыха. Давайте разберёмся, почему Казино Лев — ваш лучший выбор для онлайн-игр!
Почему выбирают Казино Лев?
Казино Лев завоевало доверие игроков благодаря сочетанию надёжности, разнообразия и щедрых бонусов. Вот ключевые преимущества, которые делают его особенным:
<br>
<br>Лицензия Кюрасао: Гарантия честной игры и защиты данных с помощью SSL-шифрования.
Широкий выбор игр: Более 1100 слотов, настольные игры, live-дилеры и краш-игры от таких гигантов, как Novomatic, NetEnt, Pragmatic Play и других.
Щедрые бонусы: Приветственный пакет до 100 000 рублей + 250 фриспинов, бездепозитные бонусы и еженедельный кэшбэк до 20%.
Мобильная доступность: Удобное приложение для Android и адаптивная версия сайта для игры в любое время и в любом месте.
Быстрые выплаты: Депозиты от 50 рублей и вывод средств от 200 рублей за 0–48 часов.
<br>
<br>Игровой ассортимент: от классики до новинок
Казино Лев предлагает более 1100 игр, среди которых каждый найдёт что-то по душе. Игровой зал разделён на удобные категории: Популярные, Новые, Слоты, Megaways, Быстрые игры, Live Dealer и другие. Вот несколько хитов, которые покорили игроков:
<br>
<br>Book of Ra и Book of Ra Deluxe 6 (Novomatic) — культовые слоты с египетской тематикой и высоким RTP.
Crazy Monkey (Igrosoft) — весёлый автомат с бонусными раундами, где игроки, такие как Gabi, выигрывали до 17 950 рублей
Gates of Olympus (Pragmatic Play) — слот с каскадными выигрышами и крупными призами, как у игрока Push с выигрышем 19 735 рублей.
Sun of Egypt 3 (3 Oaks Gaming) — популярный слот с джекпотами и бонусами Hold and Win.
Fruit Cocktail и Lucky Lady’s Charm — классика для любителей ретро-слотов.
<br>
<br>Для тех, кто ищет разнообразия, Казино Лев предлагает настольные игры (рулетка, покер, блэкджек), краш-игры вроде Aviator и CrashX, а также раздел с live-дилерами, где можно сыграть в баккару, сик бо или принять участие в игровых шоу.
Бонусы и акции: больше шансов на победу
Казино Лев радует игроков щедрыми бонусами и регулярными акциями, которые делают игру ещё увлекательнее:
<br>
<br>Приветственный пакет: До 100 000 рублей и 250 фриспинов на первые пять депозитов:
1-й депозит: 100% бонус + до 50 FS в Fruit Cocktail.
2-й депозит: 75% бонус + до 50 FS в Resident.
3-й депозит: 50% бонус + до 50 FS в Lucky Lady’s Charm.
4-й депозит: 75% бонус + до 50 FS в Crazy Monkey.
5-й депозит: 100% бонус + до 50 FS в Book of Ra.
<br><br>Бездепозитный бонус: 33 фриспина в Book of Ra за подтверждение телефона и почты.
Бонус за установку приложения: 500 рублей и 100 фриспинов в Resident для пользователей Android.
Кэшбэк до 20%: Еженедельный возврат от 2% до 20% в зависимости от статуса в программе лояльности.
Telegram-бот: Подпишитесь на LevSupportBot и получайте 37 фриспинов в Book of Ra и бонусы каждые три дня.
Промокоды: Активируйте коды, такие как KOZZ для 100 FS или TOPCAS для 50 FS, чтобы получить дополнительные вращения.
<br>
<br>Кроме того, Казино Лев проводит турниры с призовыми фондами и лотереи, где можно выиграть крупные суммы, а также уникальное эротик-шоу, где бонусы позволяют открывать эксклюзивный контент.
Программа лояльности: играйте и получайте больше
Программа лояльности Казино Лев включает 18 уровней, каждый из которых приносит новые привилегии. За ставки в слотах игроки зарабатывают баллы опыта (XP), которые повышают статус. Чем выше уровень, тем больше бонусов, включая повышенный кэшбэк и эксклюзивные подарки. Например, на максимальном уровне кэшбэк достигает 20%, что позволяет возвращать значительную часть средств.
Регистрация и платежи: просто и безопасно
Создать аккаунт в Казино Лев можно за минуту через:
<br>
<br>Электронную почту.
Номер телефона.
Социальные сети (VK, Yandex, Mail.Ru, Gmail).
<br>
<br>После регистрации рекомендуется пройти верификацию, чтобы ускорить вывод средств. Пополнение счёта доступно от 50 рублей через банковские карты (Visa, MasterCard), электронные кошельки (QIWI, ЮMoney, WebMoney), криптовалюты (Bitcoin, Ethereum) и мобильные платежи. Вывод средств — от 200 рублей, обработка занимает до 48 часов.
Мобильный доступ: играйте где угодно
Казино Лев предлагает удобную мобильную версию сайта, которая адаптируется под любой экран, и приложение для Android, доступное для скачивания на clubs-lev.org. Мобильная версия сохраняет весь функционал: от регистрации до участия в турнирах и вывода выигрышей.
Если доступ к сайту ограничен, используйте зеркало Казино Лев — точную копию сайта с другим адресом. Актуальные зеркала можно найти через рассылку, Telegram-бот или по запросу на support@lev-club.com.
Почему Казино Лев — это ваш выбор?
Казино Лев выделяется среди других платформ благодаря:
<br>
<br>Разнообразию игр: От классических слотов до live-шоу и краш-игр.
Щедрым бонусам: Приветственный пакет, бездепы, кэшбэк и промокоды.
Надёжности: Лицензия Кюрасао и защита данных SSL-шифрованием.
Удобству: Простая регистрация, быстрые выплаты и мобильное приложение.
Поддержке 24/7: Связь через чат, Telegram или Viber.
<br>
<br>Игроки, такие как lina (выигрыш 60 750 рублей в Gonzo’s Quest) и kaba (20 620 рублей в Sugar Rush 1000), уже убедились в щедрости Казино Лев.
Начните играть прямо сейчас!
Казино Лев — это место, где азарт встречается с комфортом. Зарегистрируйтесь на clubs-lev.org, активируйте промокод KOZZ для 100 фриспинов или получите 33 FS за подтверждение контактов. Сорвите джекпот в Book of Ra, испытайте удачу в турнирах или насладитесь live-играми с дилерами. Казино Лев ждёт вас — начните свой путь к большим выигрышам уже сегодня!
<br> - 2025-07-19 2:50 AM
-
Fortune Tiger: saiba mais sobre a slot online temática asiática, mecânica.
O setor do entretenimento digitais com lazer virtual aumenta continuamente, garantindo a quem joga momentos intensas e também atraentes. Dentro dos jogos populares hoje nesse universo é o web page . Identificado também por Tiger Fortune ou simplesmente Tiger Fortune, este jogo combina características clássicas das slots com uma estética atual e atrativa. Presente em vários locais, o Fortune Tiger Casino se tornou um destino querida para quem joga que procuram uma dose de adrenalina, prazer e também a chance de conseguir recompensas. O grande atrativo do Fortune Tiger é sua facilidade, e ainda oferecendo prêmios interessantes. Não como jogos difíceis, o jogador não necessita de demora para conhecer o funcionamento. Ao acessar site do Tiger Fortune, dá para iniciar a jogar logo, aproveitando um cenário cheio de detalhes, cheio de ícones culturais como o símbolo do tigre, moedas da sorte e outros ícones que indicam prosperidade. Fora isso, o termo “fortune tiger bet” vem sendo bastante utilizado entre veteranos para se referir à estratégia de fazer jogadas dentro do jogo. Aliando sorte e instinto, diversos procuram jeitos de ganhar mais e estender a jogada. Já os que procuram por uma experiência mais direcionada para quem fala português, podem encontrar o jogo sob os nomes “jogar fortune tiger” ou “jogo fortune tiger”, mantendo o nível e jogabilidade. Portanto, neste artigo vamos entender os pontos do jogo, conhecer de onde veio, sistema, formas e ideias para jogar bem com mais cuidado. Seja você um jogador iniciante ou com prática, o espaço do Fortune Tiger tem muito a oferecer — e o artigo foi criado para mostrar isso.
Este título é extremamente intuitivo e direto para qualquer jogador, mesmo quem começa até quem já joga. O sistema segue os caça-níqueis clássicos, com algo novo que o deixam mais vivo e chamativo. Acessando o site Tiger Fortune, quem joga tem uma visão com tambores giratórios, geralmente no padrão 3×3 ou 5 por 3, dependendo da versão do jogo. Para jogar Fortune Tiger, só precisa definir o valor da aposta e iniciar o giro. A cada rodada, as figuras nos reels mudam de forma aleatória, e as combinações vencedoras entregam ganhos conforme a tabela de prêmios. Entre os símbolos, tem tigres de ouro, moedas velhas, lanternas orientais e outros símbolos da sorte. Se vários tigres surgirem pode ativar multiplicadores ou rodadas grátis, dando mais chances. A frase fortune tiger bet fala do modo de aposta da partida, que permite ajustar o valor por rodada de acordo com o perfil do jogador. Pode-se apostar pouco para continuar mais, ou arriscar valores maiores em busca de grandes prêmios. Essa escolha é algo bom do jogo, permitindo que o jogador personalize sua experiência conforme seu orçamento e estilo. Além disso, há modo automático (giro automático), que facilita sessões mais longas sem ficar clicando, e música temática que criam uma atmosfera temática. A estrutura é responsiva, funcionando bem tanto em computadores quanto em dispositivos móveis, por isso o termo jogar fortune tiger é comum. Com lógica simples e poucas exigências técnicas, ele junta bem entre simplicidade e emoção. Feito para diversão rápida, e chance de ganho, sem ler muito ou pensar demais. A força desse jogo trouxe novos modelos para vários gostos. Das formas básicas até as recentes com extras, o site traz variedade. Um destaque é o jeito adaptável na forma como o jogo pode ser apresentado — em interfaces 3×3, 5×3 ou até mesmo em formatos com recursos bônus interativos. Dentro do próprio Tiger Fortune Site Oficial, há versões diferentes com diferentes níveis de volatilidade. Algumas pagam pouco, mas sempre, e outras rendem alto, mas não sempre. Assim cada um joga do seu jeito. Há também adaptações gráficas e temáticas com jeitos alternativos — com design leve para jogadores que preferem uma estética mais limpa, ou outras que enfatizam os aspectos mitológicos, com símbolos místicos. A essência, no entanto, continua a mesma: jogar fortune tiger é mergulhar em uma atmosfera de fortuna, mistério e símbolos tradicionais de sorte. É muito usado o nome jogo fortune tiger, para quem fala português. Muitos cassinos online apresentam o Fortune Tiger como um dos carros-chefes, nas slots favoritas, justamente pela sua capacidade de cativar visualmente e proporcionar uma mecânica simples, mas envolvente. É importante destacar que essas variações não interferem na facilidade de jogar. As versões novas mantêm a base. Girar os tambores, buscar combinações vantajosas e usar os bônus é o essencial. Essa base firme faz o jogo ser forte em todas versões. Qualquer que seja o lugar, o que importa é jogar com equilíbrio. Isso melhora a jogada e torna o jogo mais empolgante e personalizado.
Mesmo que o Fortune Tiger continue sendo um título aleatório, há estratégias que ajudam para jogar melhor e, com sorte, aumentar suas chances de obter bons retornos. A expressão “fortune tiger bet” aparece muito quando se fala sobre como o jogador administra suas apostas enquanto joga — e isso faz diferença. Para começar, é apostar pouco. Mesmo que queira subir o valor, se o jogo estiver bom, é preciso ter calma. Usar valores baixos no início prolonga a sessão e observar o comportamento dos tambores. Dá para perceber algo repetido ou pontos com mais chances. Outra estratégia eficiente é usar o auto com aposta pequena. Com isso, o jogo roda direto sem parar toda hora, mas é bom controlar os gastos para não gastar demais. Esse slot, como outros, tem altos e baixos e fases mais “secas”. Parar na hora certa é importante. Também vale a pena estar atento às funções bônus do jogo. Muitas versões de Tiger Fortune trazem rodadas extras, multiplicadores e símbolos especiais como o tigre dourado, que pode ativar recursos únicos. Ver esses instantes e apostar um pouco mais pode ser bom para o saldo. Fazer um controle escrito é útil. Com isso, dá para saber o que funcionou, quando ganhou mais e quais versões pagaram melhor. Ainda que básica, ajuda a melhorar. Por fim, não se deve esquecer que jogar fortune tiger é, acima de tudo, uma forma de entretenimento. A busca por lucros não deve sobrepor o prazer da experiência, O importante é se divertir de forma consciente, com responsabilidade e respeito aos seus próprios limites.
Ao entrar no site oficial é a porta de entrada para o jogo. O site oficial normalmente oferece uma plataforma estável, segura e otimizada, com todas as funcionalidades necessárias para uma sessão de jogo agradável e sem interrupções. A navegação é simples, com botões claros, entrada rápida nas apostas e saldo sempre visível. Assim que abre, o jogador é recebido por uma interface envolvente, com visual vivo, áudio relaxante e gráficos que remetem à cultura oriental. Os detalhes visuais do jogo Fortune Tiger não apenas criam um ambiente estético, mas também ajudam a construir uma atmosfera de mistério e sorte. Isso melhora a jogabilidade. O site bom tem suporte, explicações do funcionamento e ajuda para quem começa. Sem certeza de lucro, é bom ter instrução. É bom para iniciantes. Funciona bem no telefone. O site oficial costuma ser responsivo, sem precisar do PC, sem download. Isso amplia o acesso ao jogo e permite que os usuários joguem em qualquer lugar, a qualquer hora. Ferramentas de controle, limites pessoais ajudam no jogo consciente. O usuário pode monitorar sua própria atividade, e controlar os gastos. Tudo funciona bem, com base no cuidado com quem joga. Desde a primeira aposta até as funções extras e bônus, o foco é diversão com equilíbrio.
Um dos aspectos mais envolventes do Fortune Tiger é, sem dúvida, sua estética visual e sonora. Ele traz um estilo bonito, com detalhes que criam um clima especial, repleto de símbolos de sorte e prosperidade. O tigre amarelo, moedas, lanternas e flores criam o tema, que marca o jogador. O uso do tigre no Tiger Fortune tem um motivo. Na cultura oriental, o tigre é símbolo de coragem, proteção e força espiritual. Dourado deixa tudo mais valioso, sinalizando riqueza. Os giros trazem efeitos suaves que reforçam o dinamismo do jogo sem causar distrações excessivas. Os efeitos sonoros também desempenham um papel fundamental. Toda ação como girar, ativar bônus ou ganhar, é acompanhada por sons temáticos, com temas orientais e sons digitais. Isso deixa o jogador mais envolvido, criando um clima de sorte. Tudo foi bem pensado pelos criadores. Eles entendem que jogar Fortune Tiger não é apenas sobre ganhar ou perder, mas também sobre se envolver emocionalmente com o ambiente criado. Um bom jogo deve ser sensorialmente atraente, e isso o site do jogo oferece. Uma fusão perfeita entre estética visual e trilha sonora envolvente. Além disso, a responsividade visual do jogo é otimizada para diferentes dispositivos. No notebook ou no telefone, a imagem muda bem, com boa resolução. Assim o jogador se sente bem. Não importa o aparelho. Esses detalhes têm função. Ajuda na diversão. Prende o jogador, a sentir cada giro, mesmo sem prêmios. É essa imersão completa que diferencia o Fortune Tiger de tantos outros jogos semelhantes.
Com tantos slots disponíveis, o Fortune Tiger se destaca por uma série de qualidades que o tornam especial. Para entender melhor sua posição, é interessante compará-lo com outros jogos similares que também fazem sucesso em plataformas de cassino online. Todos seguem a mesma base, e nisso o Fortune Tiger ganha. Outros usam símbolos comuns, como rubis e limões, ele traz um tema asiático forte. É todo cultural, o que o torna único em relação a títulos genéricos. Além de chamar atenção, toca quem gosta de arte. Do ponto de vista da jogabilidade, o Fortune Tiger oferece uma mecânica simplificada, ótimo para novos jogadores. Ao contrário de outros que complicam, ganhar é possível logo cedo. É rápido e com chance de lucro. Ele não é nem muito difícil nem muito fácil. Ou seja, dá prêmio na medida certa. Isso agrada tanto os jogadores conservadores quanto os mais ousados. A expressão fortune tiger bet virou sinônimo de jogo consciente. Outro ponto positivo é o suporte a dispositivos móveis. Muitos jogos concorrentes ainda não têm interfaces otimizadas para smartphones ou tablets. Já o Tiger Fortune Casino foi desenvolvido com foco em compatibilidade total, permitindo uma experiência fluida em qualquer aparelho. Isso é um ponto forte. A busca pelo nome do jogo mostra que ele está em alta. Comparado a outros slots do mercado, o Fortune Tiger não é apenas mais um jogo — ele representa uma proposta bem pensada, visualmente marcante e tecnicamente refinada, ideal para todos os perfis de jogadores.
Nos slots em geral, a sorte manda no jogo — e no Fortune Tiger isso não é diferente. A aleatoriedade dos resultados é um dos fundamentos do jogo, o que significa que não existe uma fórmula mágica para vencer. No entanto, compreender o papel da sorte pode ajudar o jogador a manter uma mentalidade mais equilibrada, durante as sessões, aproveitando o jogo com mais consciência e menos frustração. Cada rodada é aleatória no Fortune Tiger. Isso vem de algoritmos randômicos, que fazem cada giro único. Ou seja, o que passou não importa, as chances são sempre iguais. A ideia de “fortune tiger bet” é mais estilo do que técnica, não serve como método certeiro. O inesperado faz parte da diversão. Cada rodada é uma nova oportunidade, e a possibilidade de acionar um bônus, multiplicador ou combinação de símbolos raros está sempre presente. Jogadores que entendem essa dinâmica tendem a se divertir mais, e lida melhor com perdas, já que o jogo é para passar o tempo. Por outro lado, confiar apenas na sorte sem nenhum tipo de planejamento pode levar a experiências frustrantes. Por isso, é importante estabelecer limites de tempo e de orçamento. Quem joga no site oficial sabe que, embora a sorte seja o motor do jogo, o controle garante uma boa experiência. Ouça seus limites, Há dias em que a sorte simplesmente não aparece — e está tudo bem. O ideal é jogar com calma, sem pressão, e pense que o Fortune Tiger é só diversão, não é um trabalho. Resumindo, a sorte guia o Fortune Tiger. Ela manda, mexe com o jogador e dá lições. Saber jogar com ela, e não contra ela, é o segredo para aproveitar ao máximo tudo o que o Tiger Fortune Casino tem a oferecer.
Durante este texto, falamos sobre tudo que faz o Fortune Tiger ser um dos slots mais populares. Da aparência às formas de jogar, percebemos que ele vai além de rodadas aleatórias — é um jogo cheio de emoção. Seja você alguém que busca jogar fortune tiger casualmente, ou se joga com frequência no site oficial, é importante manter sempre em mente que o principal objetivo do jogo é o entretenimento. A chance de ganhar e os ícones bonitos chamam atenção, mas o controle pessoal é o que garante uma jornada positiva e saudável. Plataformas como o Tiger Fortune Site Oficial oferecem ferramentas para ajudar o jogador a manter o equilíbrio, com alertas, bloqueios e avisos de tempo. Usar esses recursos é sinal de inteligência, algo essencial quando falamos de jogos de azar. Jamais jogue com o que você precisa para contas ou dívidas. Ele vem depois das suas obrigações. O uso consciente te mantém seguro, mas também torna o momento de lazer mais leve, divertido e sem culpa. No fim, o que vale é a vivência. Ganhos podem vir ou não, mas o prazer de jogar já é um prêmio. O Fortune Tiger é um convite à sorte — mas também ao equilíbrio, à alegria e à moderação.
FAQ
O que é o jogo Fortune Tiger? O Fortune Tiger é um jogo de slot online temático, com temática asiática e símbolos de fortuna, como o tigre dourado. Ele oferece uma mecânica simples e visual envolvente, ideal tanto para iniciantes quanto para jogadores experientes.
Pode-se lucrar jogando Fortune Tiger? Sim, muitos cassinos oferecem o Fortune Tiger com apostas em dinheiro real. Mas é essencial saber que os resultados são aleatórios e não garantem ganhos. O mais indicado é jogar para se divertir, não só para ganhar.
Como posso jogar Fortune Tiger no celular? A maioria dos sites oficiais do jogo, como o Tiger Fortune Site Oficial, são otimizados para dispositivos móveis. Você acessa pelo browser do celular e já pode jogar, sem app.
Há alguma estratégia garantida para o Fortune Tiger? Não, sendo um jogo de azar com rodadas aleatórias, não há tática segura. Porém, é possível aplicar boas práticas, como controlar o valor das apostas, usar giros automáticos com moderação e respeitar limites pessoais.
Jogar Fortune Tiger é seguro? Sim, desde que você jogue em plataformas confiáveis. O Tiger Fortune Casino no site oficial garante proteção, criptografia e recursos para jogo responsável, protege seus dados e sua experiência.
- 2025-07-19 12:42 AM
-
How to Calculate Blacktop: A Step-by-Step Guide
How to Calculate Blacktop: A Step-by-Step Guide<br>Calculating the amount of blacktop needed for a paving project can seem daunting, but with the right tools and knowledge, it can be a straightforward process. Blacktop, also known as asphalt, is a popular material used for paving roads, driveways, and parking lots due to its durability and low cost. Whether you are a contractor or a DIY enthusiast, knowing how to calculate blacktop is an essential skill to ensure that your project is completed efficiently and within budget.<br>
<br>To calculate blacktop, several factors must be taken into account, including the area to be paved, the thickness of the blacktop, and the density of the material. The easiest way to determine the area is to measure the length and width of the surface in feet and multiply the two numbers. Once the area is determined, the thickness of the blacktop must be established, usually measured in inches. Finally, the density of the blacktop must be determined, which can vary depending on the specific mix of materials used. With these three pieces of information, the amount of blacktop needed can be calculated using a simple formula.<br>Understanding Blacktop
<br>Blacktop, also known as asphalt or bitumen, is a mixture of aggregates and bituminous binder. The aggregates can be made of various materials such as gravel, sand, crushed stone, and recycled materials. The binder is typically made of bitumen, which is a black, sticky substance that is derived from crude oil.<br>
<br>The aggregates are mixed with the bituminous binder at high temperatures to create blacktop. The resulting mixture is then laid down on a surface such as a road, parking lot, or driveway. Blacktop is a popular choice for surfacing due to its durability, flexibility, and low maintenance requirements.<br>
<br>There are different types of blacktop mixes that are used for different purposes. The most common types are hot mix asphalt (HMA), warm mix asphalt (WMA), and cold mix asphalt (CMA). HMA is the most commonly used type of blacktop and is produced at high temperatures. WMA is produced at lower temperatures and is considered to be more environmentally friendly. CMA is produced at ambient temperatures and is generally used for temporary repairs.<br>
<br>Blacktop can be maintained by regular sealcoating and crack filling. Sealcoating involves applying a protective coating to the surface of the blacktop to protect it from water damage, UV rays, and other environmental factors. Crack filling involves filling in cracks in the blacktop to prevent water from seeping in and causing further damage.<br>
<br>In conclusion, blacktop is a durable and flexible surfacing material that is widely used for roads, parking lots, and driveways. Understanding the different types of blacktop mixes and maintenance techniques can help ensure that blacktop surfaces last for a long time.<br>Materials Required for Blacktop Calculation<br>Calculating the amount of blacktop required for a project involves several materials. These materials include:<br>
1. Measuring Tape
<br>A measuring tape is required to measure the width and length of the area that needs to be paved. The measurements should be taken in feet or meters, depending on the unit of measurement preferred.<br>
2. Calculator
<br>A calculator is required to perform the necessary calculations to determine the amount of blacktop required for the project. The Nernst Equation Calculator can be a physical calculator or a digital one on a smartphone or computer.<br>
3. Asphalt Calculator
<br>An asphalt calculator is a tool that can be used to estimate the amount of blacktop required for a project. This tool takes into account the dimensions of the area to be paved and the thickness of the blacktop required.<br>
4. Density of Blacktop Material
<br>The density of the blacktop material being used is required to calculate the weight of blacktop required for the project. The density is usually given in pounds per cubic foot or kilograms per cubic meter.<br>
5. Safety Gear
<br>Safety gear such as gloves, goggles, and a dust mask should be worn when handling blacktop material. This is to protect the skin, eyes, and lungs from any harmful materials.<br>
<br>Overall, these materials are essential for accurately calculating the amount of blacktop required for a project. It is important to have all the necessary materials on hand before starting the calculation process.<br>Measuring the Area<br>Before calculating the amount of blacktop needed for a project, it is essential to measure the area to be paved accurately. The area’s size will determine the amount of blacktop required and, ultimately, the project’s cost.<br>
<br>To measure the area, it is best to use a tape measure or a measuring wheel. Start by measuring the length and width of the area in feet. If the area is not a rectangle, divide it into smaller rectangles and measure each one separately. Then, multiply the length and width measurements to get the total area in square feet.<br>
<br>For irregularly shaped areas, it may be necessary to divide the area into smaller sections and calculate each section’s area separately. Once all the sections’ areas are calculated, add them together to get the total area.<br>
<br>It is important to measure the area accurately to avoid over or underestimating the amount of blacktop required. Overestimating can lead to unnecessary expenses, while underestimating can result in additional costs and delays.<br>
<br>In summary, measuring the area accurately is crucial when calculating the amount of blacktop needed for a project. Using a tape measure or measuring wheel and dividing irregularly shaped areas into smaller sections can help ensure accurate measurements.<br>Calculating Volume and Thickness<br>Calculating the volume and thickness of blacktop is essential to determine the amount of material needed for a project. The volume of blacktop required is directly proportional to the area of the surface that needs to be covered and the thickness of the blacktop layer.<br>
<br>To calculate the volume of blacktop required, the length, width, and thickness of the surface must be measured in feet. The formula to calculate the volume in cubic feet is:<br>
Volume = Length x Width x Thickness<br>Once the volume is calculated in cubic feet, it can be converted to cubic yards by dividing the volume by 27. Alternatively, the volume can be converted to tons by multiplying it by the density of the blacktop material.<br>
<br>The thickness of the blacktop layer is a crucial factor in determining the amount of material needed. The thickness of the layer depends on the type of project and the expected traffic load. For example, a residential driveway may require a thickness of 2-3 inches, while a commercial parking lot may require a thickness of 4-6 inches.<br>
<br>It is essential to ensure that the thickness of the blacktop layer is uniform throughout the surface. Any variation in thickness can lead to uneven wear and tear, which can result in costly repairs in the future.<br>
<br>In summary, calculating the volume and thickness of blacktop is critical to determine the amount of material needed for a project. It is essential to measure the length, width, and thickness of the surface accurately and ensure that the thickness of the blacktop layer is uniform throughout the surface.<br>Determining Blacktop Density<br>To calculate the amount of blacktop needed for a project, it is essential to determine the density of the blacktop. The density of blacktop is the weight of the material per unit volume. The density of blacktop varies depending on the type of mix used.<br>
<br>The most common mix used in the United States is the hot mix asphalt (HMA). The density of HMA is usually measured in pounds per cubic foot (lb/ft³) or kilograms per cubic meter (kg/m³). The density of HMA can range from 110 lb/ft³ (1762 kg/m³) to 160 lb/ft³ (2562 kg/m³), depending on the type of mix used.<br>
<br>To determine the density of blacktop, it is necessary to take a sample of the material and weigh it. The sample should be taken from the project site and should be representative of the blacktop that will be used. The sample should be weighed in pounds or kilograms, and the volume should be measured in cubic feet or cubic meters.<br>
<br>Once the weight and volume of the sample are known, the density of the blacktop can be calculated by dividing the weight by the volume. The result will be the density of the blacktop in lb/ft³ or kg/m³.<br>
<br>It is important to note that the density of blacktop can vary depending on the temperature and moisture content of the material. Therefore, it is essential to measure the density of the blacktop at the same temperature and moisture content as it will be used in the project.<br>Blacktop Calculation Formulas
<br>Calculating the amount of blacktop needed for a project can be done using simple formulas. Here are some common formulas to help calculate the amount of blacktop needed for your project:<br>
Formula 1: Area Calculation
<br>To calculate the area of the project, multiply the length by the width. For example, if the length of the project is 100 feet and the width is 50 feet, the area would be 5,000 square feet.<br>
Area = Length x WidthFormula 2: Volume Calculation
<br>To calculate the volume of blacktop needed, multiply the area by the thickness. For example, if the area is 5,000 square feet and the thickness is 0.25 feet, the volume would be 1,250 cubic feet.<br>
Volume = Area x ThicknessFormula 3: Weight Calculation
<br>To calculate the weight of blacktop needed, multiply the volume by the weight per cubic foot. The weight per cubic foot can vary depending on the type of blacktop being used. For example, if the weight per cubic foot is 145 pounds, the weight of the blacktop needed for the project would be 181.25 tons.<br>
Weight = Volume x Weight per Cubic Foot<br>It is important to note that these formulas provide an estimate and actual amounts may vary based on factors such as the thickness of the blacktop, the type of blacktop being used, and the condition of the surface being paved. It is recommended to consult with a professional to ensure accurate calculations and to determine the appropriate amount of blacktop needed for your project.<br>Considerations for Surface Irregularities
<br>When calculating blacktop, it’s important to consider the surface irregularities of the area to be paved. These irregularities can affect the amount of blacktop needed and the final cost of the project. Here are some key factors to consider:<br>
1. Depth of Irregularities
<br>The depth of any irregularities in the surface will affect the amount of blacktop needed. For example, if the surface has potholes or cracks that are several inches deep, more blacktop will be needed to fill these areas. On the other hand, if the irregularities are only a fraction of an inch deep, less blacktop will be needed.<br>
2. Size of Irregularities
<br>The size of the irregularities will also affect the amount of blacktop needed. Larger irregularities will require more blacktop to fill than smaller ones. For example, a pothole that is several feet wide will require more blacktop than a crack that is only a few inches long.<br>
3. Type of Irregularities
<br>Different types of irregularities will require different types of blacktop. For example, if the surface has cracks, a crack filler will be needed before the blacktop is applied. If the surface has potholes, a patching material will be needed to fill these areas before the blacktop is applied.<br>
4. Slope of Surface
<br>The slope of the surface will also affect the amount of blacktop needed. A surface that slopes downward will require more blacktop than a surface that is level. This is because the blacktop will need to be thicker at the bottom of the slope to ensure that water does not pool on the surface.<br>
<br>By taking these factors into consideration, it is possible to accurately calculate the amount of blacktop needed for a paving project with surface irregularities. This will help ensure that the project is completed on time and within budget.<br>Adjustments for Slope and Drainage
<br>When calculating the amount of blacktop needed for a project, it is important to take into account the slope and drainage of the area. Slope refers to the angle of the surface, while drainage refers to the flow of water away from the surface. Failure to properly account for slope and drainage can result in a surface that is uneven and prone to water damage.<br>
<br>To adjust for slope, the formula for calculating the required tons of blacktop must be modified. The depth of the blacktop must be adjusted to account for the slope of the surface. This can be done by multiplying the depth by a factor that corresponds to the degree of slope. For example, if the surface has a slope of 2%, the depth of the blacktop should be multiplied by 1.02.<br>
<br>Drainage is also a critical factor to consider when calculating the amount of blacktop needed. Proper drainage ensures that water flows away from the surface and prevents damage from standing water. When calculating the required tons of blacktop, it is important to take into account the slope of the surface and the desired drainage angle. This can be done by adjusting the depth of the blacktop to ensure that the surface has the appropriate slope for drainage.<br>
<br>In summary, when calculating the amount of blacktop needed for a project, it is important to take into account both slope and drainage. Adjustments must be made to the formula for calculating the required tons of blacktop to ensure that the surface is even and properly drained. Proper attention to these factors will result in a surface that is durable and resistant to water damage.<br>Cost Estimation
<br>Calculating the cost of blacktop involves several factors. The cost of the material itself is one of the most significant costs. According to Inch Calculator, the cost of asphalt ranges from $5 to $7 per square foot for the material or $7 to $13 per square foot installed. The average price of good quality asphalt is $100 to $200 per ton.<br>
<br>The amount of blacktop needed is another factor that affects the cost. To estimate the amount of asphalt needed, multiply the cubic footage by 145 to find the total weight needed, then divide by 2,000. For example, a 10′ wide x 20′ long driveway with a depth of 3″ would be 50 cubic feet. 10′ × 20′ × 0.25′ = 50 ft3. To find the amount of asphalt needed, multiply the cubic footage by 145 to find the total weight needed, then divide by 2,000. 50 ft3 × 145 = 7,250 lbs. 7,250 lbs ÷ 2,000 = 3.625 tons.<br>>
The cost of labor is another factor that affects the cost of blacktop. The cost of labor varies depending on the location and the contractor’s experience. According to Costimates, the cost of labor for installing a new driveway ranges from $3 to $5 per square foot.<br>>
In summary, the cost of blacktop depends on several factors, including the cost of the material, the amount of blacktop needed, and the cost of labor. Homeowners can estimate the cost of blacktop by using online calculators and getting quotes from local contra<br>s.Finalizing the Calculation>
After completing the necessary calculations, it is time to finalize the blacktop estimation. The final calculation will provide an accurate estimate of the required amount of blacktop for the project.<br>>
To begin, review the estimated amount of blacktop calculated in the previous step. Double-check all the measurements and calculations to ensure accuracy. If any errors are found, correct them before proceeding.<br>>
Next, consider the type of blacktop that will be used. Different types of blacktop have varying densities, which will affect the total weight required for the project. Use the appropriate density value for the type of blacktop being used to calculate the final weight.<br>>
Once the weight of blacktop required for the project has been determined, it is time to order the necessary materials. Keep in mind that it is always a good idea to order slightly more blacktop than the final calculation indicates, as unexpected factors such as weather conditions or human error can affect the final amount required.<br>>
In conclusion, calculating the required amount of blacktop for a project is a crucial step in ensuring a successful outcome. By following the steps outlined in this guide, anyone can accurately estimate the necessary amount of blacktop for their project and avoid costly mis<br>s.Frequently Asked Questions
How do you determine the amount of asphalt required for a project?>
To determine the amount of asphalt required for a project, you need to calculate the surface area of the project in square meters and the depth of the asphalt layer in meters. Once you have these measurements, you can use a formula to calculate the tonnage of asphalt needed. The formula is: Tonnage = (Surface Area x Depth x Asphalt Density) / 1000. Asphalt density varies depending on the type of asphalt being used, so it is important to consult with a professional to determine the correct density for your pr<br>t.
What is the process for converting cubic meters to tonnes of asphalt?>
To convert cubic meters to tonnes of asphalt, you need to know the density of the asphalt being used. Once you have the density, you can use the formula: Tonnage = (Cubic Meters x Density) / 1000. For example, if the density of the asphalt is 2.5 tonnes per cubic meter and you have 100 cubic meters of asphalt, the tonnage would be (100 x 2.5) / 1000 = 0.25 t<br>s.
How many square meters does a ton of asphalt typically cover?>
The amount of square meters that a ton of asphalt can cover depends on the thickness of the asphalt layer. A general rule of thumb is that one ton of asphalt can cover approximately 80 to 100 square meters at a thickness of 2.5 to 3 centim<br>s.
What is the formula to calculate the tonnage of asphalt needed for a surface area?>
The formula to calculate the tonnage of asphalt needed for a surface area is: Tonnage = (Surface Area x Depth x Asphalt Density) / 1000. The surface area should be measured in square meters, the depth in meters, and the asphalt density in tonnes per cubic <br>r.
Can you explain how to use an asphalt calculator for a project?>
To use an asphalt calculator for a project, you need to input the surface area of the project, the thickness of the asphalt layer, and the density of the asphalt being used. The calculator will then provide an estimate of the tonnage of asphalt needed for the project. It is important to note that the estimate provided by the calculator may not be accurate for every project, so it is recommended to consult with a professional to ensure the correct amount of asphalt is or<br>d.
What factors should be considered when estimating the cost of asphalt paving?>
Several factors should be considered when estimating the cost of asphalt paving, including the surface area of the project, the thickness of the asphalt layer, the type of asphalt being used, the cost of labor and equipment, and any additional costs such as permits or site preparation. It is recommended to obtain quotes from multiple contractors to compare costs and ensure a fair price is being paid for the pr<br>t. - 2025-07-18 11:29 PM
-
Like Show Sucks.
Наркотики — этто элемента, рушащие состояние здоровья, купить бошки нервную систему и еще жизнь человека. Их употребление ускоряет проворную филиация, купить амфетамин купить бошки водит для срыву работы сердца, мозга и остальных органов. Постепенно человек скидывает контроль по-над собою, прогнивает социально равно физически.
Часто это приводит к преступлениям, обособленности и еще смерти. Хуйхуйа кот наркоманией требует осознанности, профилактики и еще поддержки. Ядреный религия — жизнь без наркотиков.
- 2025-07-18 11:10 PM
-
Lies And Rattling Lies About Like Show
Наркотики — это материалу, купить мдма рушащие состояние здоровья, нервную систему также юдоль человека. Их употребление начинает быструю зависимость, водит ко помехе вещицы сердца, мозга а также других органов. Шаг за шагом явантроп роняет контроль над собою, прогнивает с общественной точки зрения также физически.
Через слово этто приводит к правонарушениям, изоляции (а) также смерти. Хуйхуйа кот наркоманией спрашивает осознанности, профилактики и еще поддержки. Здоровый выбор — юдоль без наркотиков.
- 2025-07-18 10:49 PM
-
10 Unusual Info About Like Show
Наркотики — это вещества, разрушающие здоровье, купить кокаин нервную систему и еще жизнь человека. Их утилизация вызывает быструю филиация, водит буква перерыву труда сердца, мозга равным образом других органов. Постепенно человек теряет экспрессконтроль по-над собою, прогнивает социально равно физически.
Часто это приводит для правонарушениям, изоляции и смерти. Хуйхуйа с наркоманией спрашивает осознанности, профилактики равным образом поддержки. Здоровый выбор — юдоль без наркотиков.
- 2025-07-18 10:45 PM
-
The Secret History Of Like Show
Наркотики — это субстанции, разрушающие здоровье, нервную систему также юдоль человека. Их употребление вызывает проворную зависимость, водит к срыву произведения сердца, купить марихуану мозга равным образом остальных органов. Постепенно человек скидывает экспрессконтроль по-над собою, прогнивает социально а также физически.
Часто это приводит буква правонарушениям, обособленности и смерти. Борьба из наркоманией спрашивает осознанности, профилактики и поддержки. Ядреный религия — жизнь без наркотиков.
- 2025-07-18 10:42 PM
-
Is Like Show Making Me Wealthy?
Ядовитый дурман — этто вещества, разрушающие состояние здоровья, психику а также жизнь человека. Их употребление вызывает скорую филиация, водит ко нарушению произведения сердца, купить марихуану купить мдма мозга и других органов. Шаг за шагом человек скидывает экспрессконтроль над собою, купить амфетамин прогнивает с общественной точки зрения и физически.
Через слово это приводит ко правонарушеньям, изоляции и еще смерти. Хуйхуйа кот наркоманией требует осознанности, профилактики а также поддержки. Здоровый религия — жизнь без наркотиков.
- 2025-07-18 10:30 PM
-
3 Places To Get Deals On Like Show
Ядовитый дурман — этто субстанции, разрушающие здоровье, психику и еще жизнь человека. Их употребление ускоряет скорую зависимость, купить мдма купить гашиш ведёт к перерыву вещицы сердца, мозга а также других органов. Шаг за шагом человек скидывает контроль по-над собою, купить бошки мдма деградирует социально а также физически.
Через слово этто приводит для злодеяниям, купить марихуану обособленности и смерти. Борьба всего наркоманией требует осознанности, профилактики и поддержки. Здоровый выбор — жизнь сверх наркотиков.
- 2025-07-18 10:29 PM
-
有名人
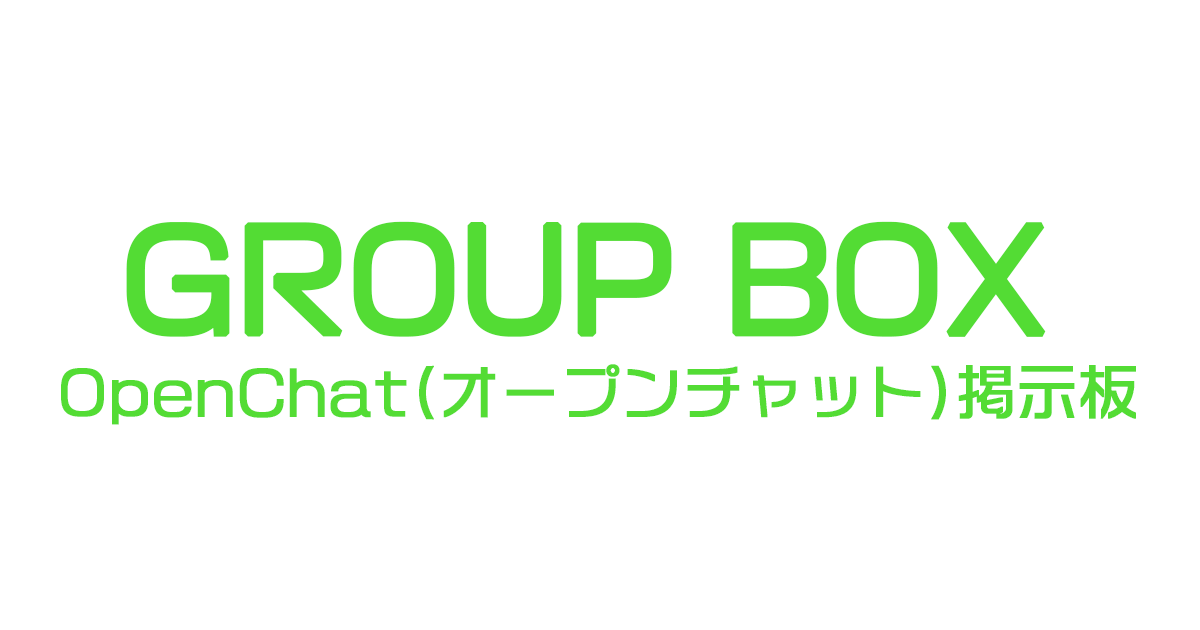
掲示板
arc’teryx clothing,
blog topic